The word busbar is a general term referring to a metallic strip or rod used as an electrical conductor. The term can also refer to a busway or busduct system, used to make complicated power distribution much easier, less expensive and more flexible. This article explores how busbar systems work, and the common questions asked when choosing an electrical power distribution solution.
- What is a busbar?
- Where are busbars used?
- Why use copper busbars?
- Why U-shaped busbars?
- What is the cost of ownership for busbars?
- Do busbars promote energy efficiency?
- Is power monitoring available for busbar systems?
What is a busbar?
Busbars, also known as busbar trunking systems or busway, distribute electricity with greater ease and flexibility than some other more permanent forms of installation and distribution. Sometimes spelled bus bar or buss bar, they are constructed of metallic strips of copper, brass or aluminum that both ground and conduct electricity.
Different coating materials provide different conductivity limits and variations in the length of a product's useful life. Busbars also come in multiple shapes and sizes, which affect the ampacity of the product. Ampacity refers to the maximum amount of electric current a conductor can carry before sustaining critical levels of deterioration.
Busbars can either be fully enclosed or designed with continuous access along an open channel. Fully enclosed busbars provide similar benefits of reduced installation time and increased performance while supporting higher ampacities.
Other reasons that busbars are popular include:
Reduced installation costs- Busbars require less construction labor, making installation less expensive due to reduced need for outside labor and electrical specialists.
Faster installation- With its modular design, setting up busbar is simpler than installing conduit or pipe and wire, requiring fewer terminations and coming together without special tools.
Flexibility for the future- Access to power can be added or modified without de-energizing the system and without an electrician. Busbar systems can also be disassembled and reused in an alternate location.
More sustainable- Busbar is considered more sustainable than conduit or cabling because it requires fewer installation materials and both the track and plug-in units are reusable and relocatable.
More efficient- Busbar is considered more efficient than cabling due to its lower voltage drop and power loss. Advancements to the structural integrity of busbar systems have also proven changing the shape of the copper busbar to increase surface area improves efficiency, exposing more of the copper surface area for a balanced load at higher ampacity.
Where are busbars used?
Busbar systems are used to safely implement three-phase power distribution systems in commercial and industrial environments. Busbars are commonly used in:
- Factories
- Data centers
- Retail facilities
- Laboratories
- Universities
- Hospitals
- EV and fleet charging stations
- Commercial buildings
Busbars range greatly in size and ampacity. Common commercial and industrial busbar sizes include 40, 50, 60, 100/160, 225,250,400, 600/630, 800, 1000, and 1200/1250 amps.
For applications in which higher ampacity is required, high power busbar systems can provide up to 6300 amps. Common high power busbar amperages include: 630, 800, 1000, 1250, 1600, 2000, 2500, 3200, 4000, 5000, and 6300 amps.
Why use copper busbars?
Copper is a common conductive metal used in busbars and many electrical utilities around the world. Copper is chosen for its resilience to higher temperatures, resistance to corrosion, and tensile strength.
The benefits of utilizing copper busbar include:
- High conductivity
- Resistance to damage
- Higher performance in clamped joints
- Lower coefficient of linear expansion
- Long lifespan
- High recovery value
- Higher modulus of elasticity
Its long-term reliability when compared to aluminum. [The surface of copper naturally oxidizes forming a thin hard layer on the surface which remains conductive. Exposed aluminum surfaces also form an oxidized film, which is not conductive and leads to long-term reliability issues with joints.]
Why are U-shaped busbars popular?
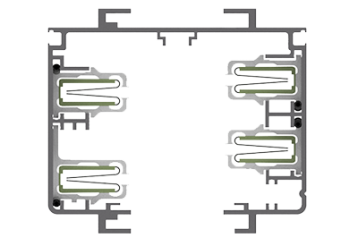
U-shaped busbar systems deliver continuous and reliable connections to power while maximizing the potential tappable locations for power access. The U-shape supports even weight distribution, mitigating any distortion resulting from excessive force and eliminating the need for routine maintenance. This system enables simple expansion, reconfiguration, or relocation to modify power distribution for new operations.
What is the cost of ownership?
Cost of ownership following installation of busbar systems is often low because overhead systems remove the need for additional construction and electrical work. With Starline systems, when a new connection to power is needed, an additional plug-in unit can be inserted anywhere along the existing open-access slot.
Plug-in units can be customized to your needs, enabling specific expansion projects and simple relocation. Relocating the busway track is so simple that it can be completed by in-house employees rather than electricians. Standard electrical systems may have lower material costs than busbar for initial installation, but lifetime costs of busbar will ultimately be much lower.
Do busbars promote energy efficiency?
Busbars can be used to conduct any form of electrical current from any type of grid. They are frequently used in high ampacity applications due to their high electrical conductivity and minimal energy loss, resulting in greater efficiency. They also give off less heat than cabling and improve airflow by placing cabling overhead, helping reduce cooling workloads.
Is power monitoring available for busbar systems?
Analysts continue to rank energy efficiency as a top concern of industrial organizations and corporate teams. However, you simply can't improve energy efficiency if you're not measuring it. Without a baseline, it is impossible to determine where to optimize, or to show improvement to management, government agencies, or customers.
By measuring power usage, you can:
- Identify current power costs and set a baseline
- Identify potential cost savings and set goals
- Implement efficiency improvement projects
- Continuously measure to determine success
Some busbars offer power monitoring. The Starline Critical Power Monitor (CPM) can be used as a standalone system mounted to electrical panels, or can also be incorporated into busway end feeds and branch-circuit applications to measure the amount of power being drawn. Features of the CPM include:
- Modular capability for connecting to mains of varying size and specification (voltage and current levels).
- Modular capability for connecting to branch circuits.
- 60-1200 amp capacity configurations.
- Ability to monitor single phase, two phase, three phase, and three phase with neutral.
- Ability to measure power, power factor, frequency, Volt Amperes, Watt hours, Volts (each phase), current (each phase) current (neutral), reactive power, and temperature. Calculates minimum and maximum values for power, Volts and current.
- Ability to set minimum and maximum alarm trigger levels for current in amps for each phase.
- Capability to integrate with any building management systems (BMS) or DCIM, with ability to transmit data over an RS-485 link, wired ethernet 10/100 link, or over a wireless mesh network.
Monitoring solutions used in busbar systems provide seamless data from a brief overview down to the individual outlet level. Power usage data can be accessed locally or remotely, allowing you to make purposeful energy efficient decisions.
Power monitoring helps to identify load imbalance before it impacts your equipment’s performance. Continuous monitoring allows you to capture changes due to new equipment and address a potential problem before downtime occurs. Being aware of power usage enables your company to scale with precision.